What’s the number one question you should be asking your solar monitoring tools?
If you are operating a portfolio of distributed energy systems, chances are that you’re interacting with a number of different inverter manufacturers, and relying on the data from the cloud-based monitoring systems that they provide.

One critical question to ask if you are relying on these different data sources is, “Do all of the monitoring tools you use report on energy the same way?”
Almost certainly the answer is “no”. Of course, the devil is in the details. And these can be some pretty expensive details.
“Counter” binning problems with energy counters
The Challenge
By far the most pernicious problem that the major inverter brands and their monitoring portals face is how to deal with gaps in binned data. This can result in under-reported energy generation, which leads to misunderstanding asset performance and sometimes even failing to recognize revenues.
What do we mean by “binned data?” It’s common for monitoring platforms to pre-calculate values that are used in reports or dashboards in “bins”. Instead of having to pull thousands of records from every minute (or second, or millisecond) and sum up a day's worth of energy, portals will have a table with the value pre-calculated per hour - a one-hour “bin.” It makes the reports load more quickly to just sum up the values in the 24 hourly bins to get a day’s total. A background process would go in and sum up all of the samples in each hour, calculate the total for each hour and store that hourly total in the correct bin.
The trouble comes when there is a data gap; for instance, due to a prepaid sim in a 4g modem at remote mini-grid location that exhausted its balance, or any other data issue.
If the reporting tool had the value 80 kWh for 10 AM, no value for 11 AM (due to a data gap), and 90 kWh for noon, and the reporting tool were asked for the total of those three hours it would report 170 kWh - which isn’t the full picture. The same gap will impact all the relevant totals for the day, the week, even the month - they will all be missing the generation from 11 AM.
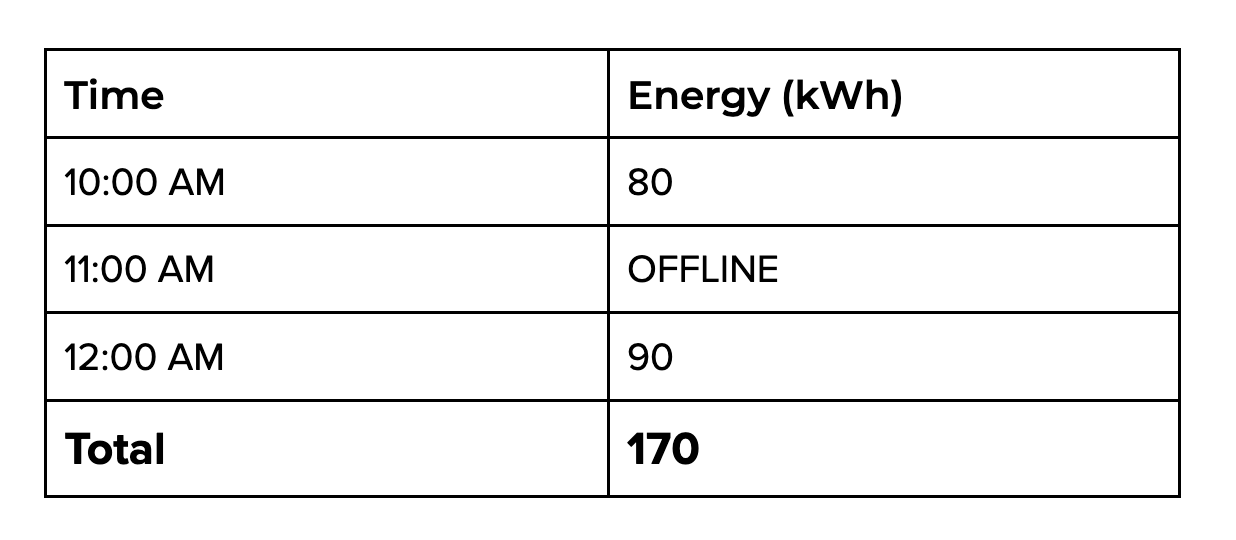
Some monitoring tools try to make data gaps obvious, to reduce the likelihood of user error - but not all of them do. In fact, some of the monitoring systems actively minimize the appearance of data gaps, visually downplaying them.
What’s worse, an astonishingly large number of the monitoring tools are missing the logic needed to remedy this situation; and some that do make an effort do it poorly.
One Solution
From the beginning, when dealing with these discrepancies, Odyssey’s system has leveraged counter values from energy meters to fill in these gaps. Electricity meters and inverters often maintain a counter that keeps a running total of how much energy a system has created - like the odometer in a car, the number should only ever go up as more energy is created.
If we go back to the previous example, but this time add in the energy counter values from the system too, the solution becomes obvious:
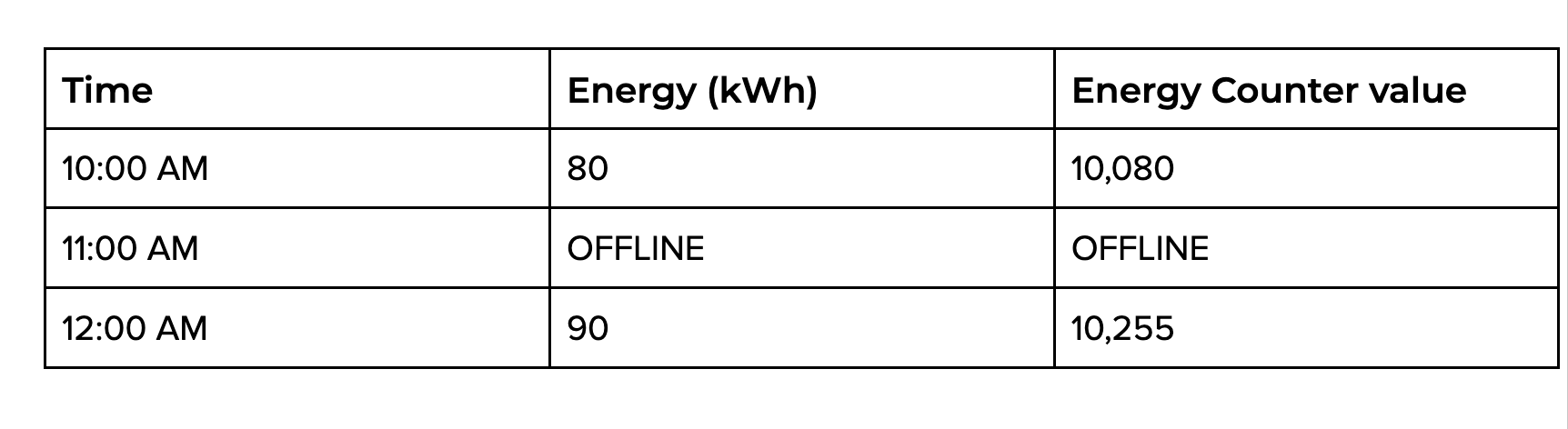
While the bin for 11 AM might be empty, if you look at the counter value we got at noon, we can deduce a value for 11 AM after all. Since the counter value at noon was 10,255, and during that hour we generated 90 kWh, and the last known counter value for 10 AM was 10,080 then we must have generated 85 kWh in between (10,255 - 90 - 10,080 = 85).
Given the literal calculus that monitoring platforms have to do in order to come up with the energy values based on a set of power values, it's surprising that this comparatively simple arithmetic often gets missed, and with costly consequences. Multi-day outages aren’t unheard of, and we’ve seen this particular problem scale up to losing days worth of production billing at a time, many times per year, adding up to as much as 5 or 10% of a system’s annual revenue.
One inverter platform seems to have a confusing “worst of both worlds” approach; instead of going back and placing the missing generation in the right place, or at least close to where the gap was discovered, they simply create a large “spike” of generation at the end of a particular reporting period to force the summed generation values to match the counters. This does true-up that reporting period to the counter, but mis-attributes the energy to the wrong hourly bins (and usually in the wrong day and even week), which could mean that it’ll be accrued at the wrong tariff (due to a change, or time of use semantics). It also can create confusingly high spikes, leading reporting users to wonder “how on earth did this 10 MW system suddenly produce 3,000 mWh in one day?”
Go “back to the drawing board” to detect meter placement issues
Meters in the wrong place or installed incorrectly can also cause frequent challenges with asset reporting. We’ve seen meters installed in the wrong place, installed “upside down” (ingress vs egress swapped), and misconfigured in the monitoring platform all with confusing consequences.
One interconnected mini-grid system (a solar mini-grid that also has a connection to another grid as backup) was mis-attributing remote grid consumption as community load. It turned out that they had placed a meter on the AC bus in such a way that both ingress from the remote grid and egress to the minigrid’s community were both being counted as community load.
As a result, any time this mini-grid needed to draw energy from the remote grid, the monitoring system would incorrectly inflate the community’s load (and thereby the transmission losses) by the amount drawn. As you can imagine, this led to confusing, periodic discrepancies which threw off revenue projections.
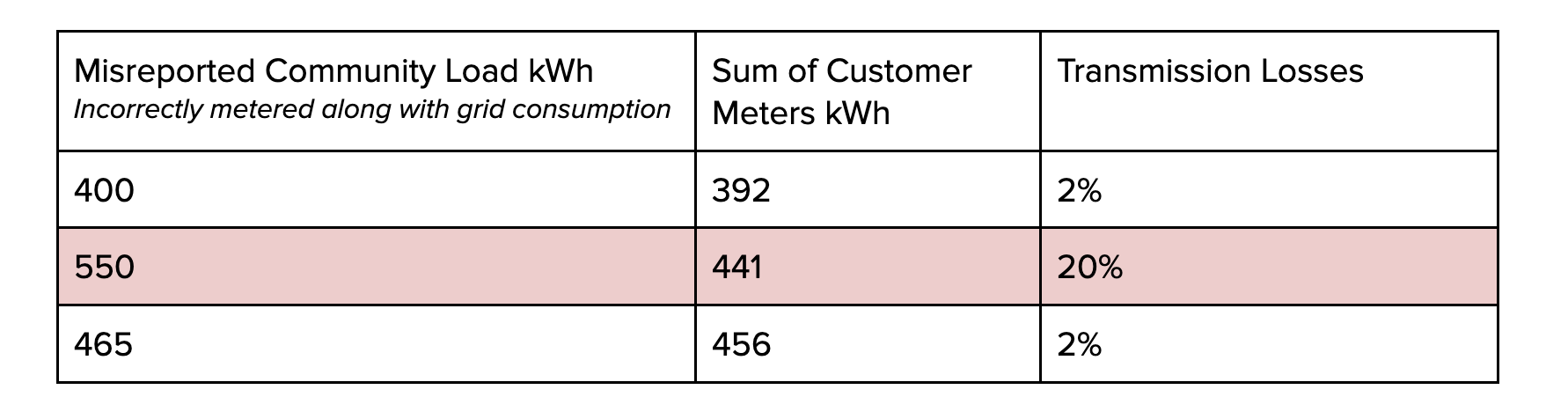
When transmission losses are periodically high, this can lead to the suspicion of theft. However, with careful analysis by our power engineers we spotted the correlation between remote grid consumption and the larger differences.
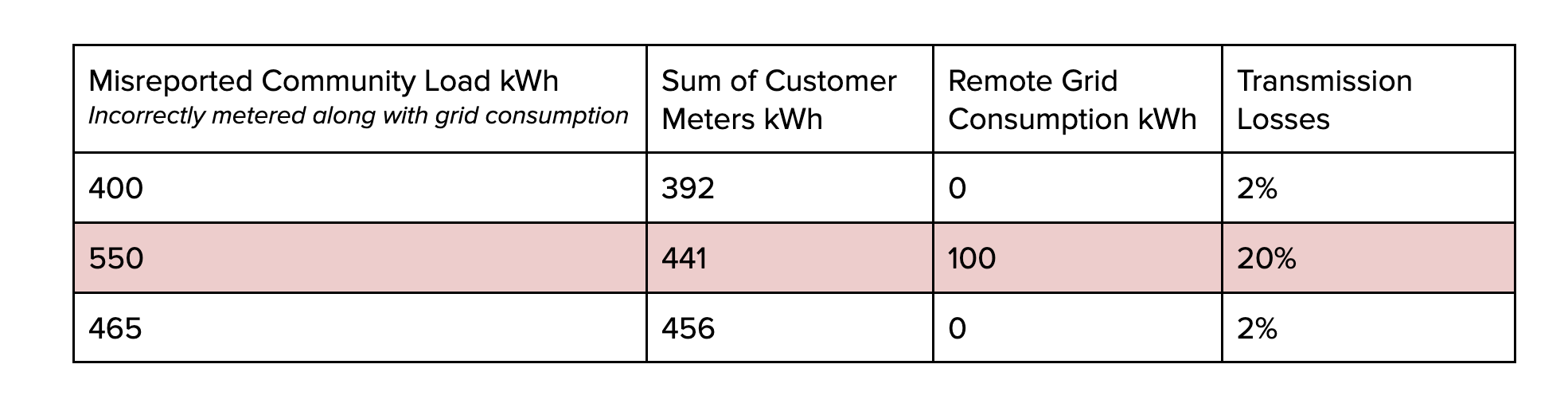
Reviewing a system’s “OT” for issues
When we add our monitoring capabilities to an existing system, our power engineers always pay close attention to the Operational Technology (OT) on the site. Often, a more complex mini-grid may have a small local network to connect sensors, controllers and loggers, and misconfigurations here can cause havoc. One particular issue that can come up is around how that network is configured.
Just like your home network, each device needs a separate address, and often those are provided to the device dynamically by the internet router; this is known as “DHCP”, the dynamic host configuration protocol, and it works the same way on a mini-grid as it does with your home network. When your iPad connects, it's assigned one IP, your phone another, your printer a third and so on. Tomorrow, your iPad might get a different address than it did today, but that doesn’t really matter as long as it can connect to the Internet.
In an OT network each IP address might refer to a specific logger, meter or controller. If those devices are configured dynamically, it can mean that the power meter you are talking to today might have a different address tomorrow - which is a big problem - because the monitoring system isn’t told that the IP has been updated - resulting in data being mis-attributed to the wrong point in the system. The plant doesn’t shut down in this case, it continues to operate - but the monitoring system is suddenly getting very wrong values.
This particular issue can result in wild swings; the meter that was reporting on the diesel generator yesterday is now being logged as though it was the feed from the PV inverter.
How Odyssey combats data issues for your DRE assets
From the beginning, a core mission of Odyssey’s remote monitoring and control technology has been to help operators streamline data, no matter what device it comes from. Here are a few ways we do that:
- Odyssey’s delivery team always has a power engineer carefully review each system, building up a model from single line diagrams and other documentation, and then comparing that against system actuals during system onboarding, often spotting and resolving misconfigurations the customer wasn’t aware of
- Adding simple but powerful fixes for data gaps, which is especially important in rural areas in emerging markets
- By analyzing and even working with you to repair the configuration of your OT networks to prevent issues down the road
- By knowing the quirks and differences between various inverter manufacturer portals and APIs, and bridging the gap to always deliver correct data
- By integrating both directly with hardware and through API, Odyssey ensures you have the full picture of your system in easy-to-read dashboards
If you’ve noticed data issues, or feel you don’t have the full picture of your asset operations, don’t hesitate to reach out.